How to Choose the Best Industrial Humidifier for Commercial Building Projects
HVACTypes of Industrial Humidifiers
There are two main categories of industrial humidifiers. The first to be developed was isothermal humidifiers that use heat to generate steam which is then put into the ventilation system. The initial systems involved taking steam from existing gas-to-steam processes or space heating boilers. However, the chemicals added to the boiler water to prevent corrosion can be unsafe for humans to breathe. Other ventilation systems then developed using the boiler steam to boil other water (steam-to-steam), as well as gas-fired or electrically heated systems. These ventilation systems are ideal for certain uses, but they require a large amount of energy to produce the steam and additional energy may also be needed to cool the air down again.
A second category, the adiabatic industrial humidifier, has gradually evolved over time and, unlike isothermal humidification, humidifies the air without adding heat. They require a fraction of the energy of any of the isothermal methods, can provide more precise humidity control, and cool down the surrounding air through evaporative cooling thereby reducing the load on air conditioning systems. Within the adiabatic humidification category, there are a variety of different systems. The ultrasonic commercial humidifier, for instance, uses a high-frequency piezoelectric disk to cause cavitation on the surface of the water and thereby produce a fine mist. This technology is frequently used in household units and smaller-scale commercial and industrial projects. Other systems involve compressed air atomizers and centrifugal atomizers.
High-pressure fogging is another type of adiabatic method with many commercial, industrial, and agricultural applications, for instance, fog humidification systems are ideal for HVAC installations requiring over 200 lbs of water per hour. This method is gaining in popularity due to its low operating cost, low environmental impact, controllability, and ease of incorporation into existing HVAC installations. This is why HVAC systems are becoming a more popular aspect of the process.
Figure 1 “The Energy Cost Comparison Chart” shows the energy costs for various humidification systems, taking the cost of power at ten cents per KW hour for 3500 hours of operation, with 1000 lb per hour moisture output.
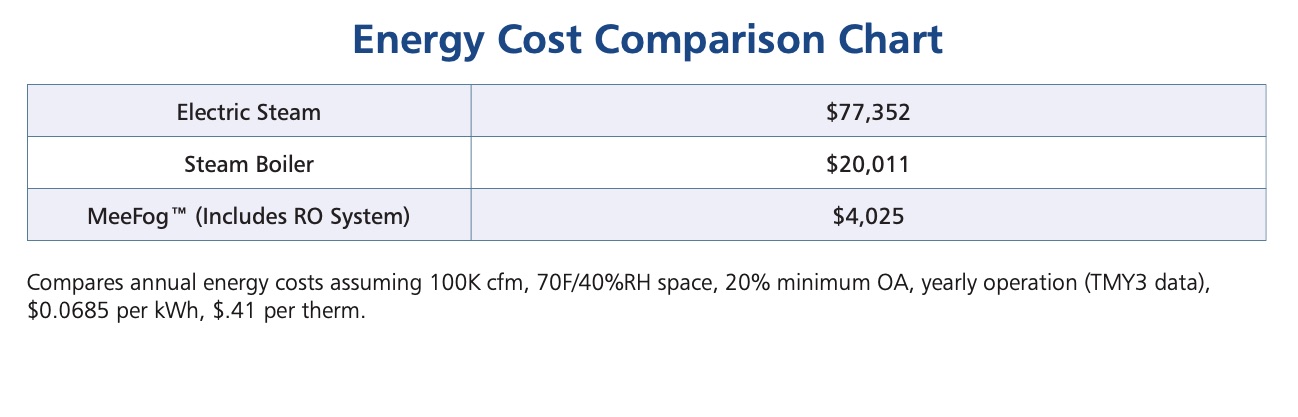
Figure 1, Energy and Cost Comparison of Humidification Systems
Sizes of Industrial Humidifiers
Fog systems inject a fine spray of purified water into the airflow. Most of the water spray evaporates, so it both cools and humidifies the airflow. There is usually not sufficient time for all the water droplets to evaporate, so a droplet filter is installed downstream of the fog nozzles. Unevaporated fog droplets collect on the filter and the captured water is drained away. The fog nozzles are installed downstream of the heating coil to ensure there is always enough heat for evaporation of the water spray.
When calculating the system needs there are several factors to consider including:
- The desired temperature and humidity in the conditioned space.
- The size of the space to be conditioned.
- The ambient air temperature and humidity during the times of day and seasons when humidification will be used.
- The amount of air moved by the air handling system.
- Percentage of outdoor air in the ventilation system.
- Features of the building/space envelope – the amount of outside air that enters through doors, windows, cracks, etc.
- Other sources of humidity in the space including people, equipment, and industrial processes.
Fog system output is controlled by opening and closing staging valves that allow high-pressure water to flow to the fog nozzles. Fog systems usually have between 3 to 15 stages of output. The fog staging level is controlled by the Building Automation System. Steam humidification systems can be gas or electric boilers, installed close to the air handling unit (AHU) with a steam dispersion manifold installed inside the AHU. Steam commercial humidifiers can also use a stream from a boiler that may be located some distance from the AHU. However, boiler steam often has hazardous corrosion inhibiting chemicals in it, so a heat exchanger is used. A boiler stream is used to boil purified water and the resulting steam is fed to a dispersion manifold located inside the AHU. Steam systems are controlled by modulating a steam throttling valve or by turning an electric immersion heater on and off.
Fog Technology
A typical fog humidification installation in an AHU consists of high-pressure pumps, a control system, fog nozzle manifolds, a fog droplet filter, a drip tray, and a drain pan (See Figure 2, Schematic of Typical Fog Installation), as well as staging valves.
High-pressure Pump Units for Industrial Humidification
Only pressurized water (1,000 to 2,000 psi) can deliver the micro-fine droplets required in humidification. High-pressure pumps, therefore, supply water to the fog nozzles in the AHU. These are generally ceramic plunger pumps with stainless steel or bronze heads, operated at low speeds to reduce noise and vibration. All units have totally enclosed fan-cooled electric motors.
Control System
Control systems are available either with simple on/off switches or variable speed drives which alter the fog output according to humidity demand. Variable speed drives are needed where the level of moisture is high. They control the capacity of fog by changing the pressure of the fog spray to prevent over-saturation of the air. Also, optional high-pressure solenoid valves allow for staged output or for the operation of separate fog zones from one pump unit.
This concept can be applied for capacity control in several AHUs in close proximity hooked up to one pump unit, making an extremely cost-effective installation. For example, one U.S. Post Office site in Washington, D.C. uses a variable speed drive for capacity control in a 150,000 CFM AHU with an air velocity of 500 feet per minute and 2300 pounds of water added per hour. This amounts to 24.5 grains of moisture per pound of air moved. Sensors in the treated space control the level of fog output. An additional high-limit sensor in the air leaving the fog chamber, usually set at 85 percent rh, ensures that there is no wetting of the ducting.
Staging Valves
Fog systems usually have multiple staged nozzle lines with each line having a set flow rate for that stage provided by multiple nozzles, output is controlled by opening and closing staging valves.
Fog Nozzles Manifolds
The usual nozzle manifold consists of half-inch OD tubes, with the nozzles evenly spaced within the cross-section of the AHU. Such an open latticework of small pipes does not impede airflow and pressure drop is negligible. For best results, stainless steel impaction pin nozzles with replaceable filters for easy maintenance should be used (See Figure 3, Fog Nozzle).
Orifice diameters of from five to seven-thousandths of an inch produce more than five billion super-fine fog droplets per second (droplets have a mean diameter of 10 microns). This provides adequate humidification while keeping energy and water waste to a minimum.
Fog Droplet Filter
In applications where a little water in the air handling system would not be problematic, a fog droplet filter may not be required. However, in most situations, the droplet filter should be positioned downstream of the nozzle manifold. It is best to tilt the fog droplet filter at a 15-degree angle to the vertical to allow for water that coalesces on the filter to flow down to the drain pan. Properly applied, fog droplet filters prevent any possibility of wetting in the ducting.
Drip Tray and Drain Pan
Both the drip tray and drain pan, which collects all unevaporated fog droplets, are usually fabricated by the HVAC contractor who then has the ability to install a great HVAC system. Drip trays should be constructed of stainless steel sheet metal of a suitable gauge and they must have a slight slope in order to carry water to the drain pan. The drip tray extends from below the fog nozzles to the drain pan. The drain pan should be installed directly under the fog droplet filter and plumbed directly to the building’s drainage system.
Water Supply
Reverse Osmosis (RO) treated water is often used in fog humidification to prevent mineral dusting of the treated areas. In some areas, however, where the local water supply is of sufficient quality, RO water is unnecessary. Contractors are advised to use the water lab facilities of a reputable fog system vendor. Often, free water testing and advice are available.
Applications of Industrial and Commercial Humidification

Due to its low operating cost and controllability, high-pressure fogging humidification systems are an energy efficient alternative to traditional steam humidifiers. Not only can fog humidification save you energy and money compared to steam, it is also easier to maintain.
Humidification plays a vital role in maintaining indoor air quality for the healthcare industry; however, with growing public concern over indoor air quality and a heightened awareness of the impact of humidity on industrial and commercial environments, many new projects face the problem of how best to incorporate humidification.
Fog humidification in air handling units (AHUs) is one alternative. As mentioned in the video above, MeeFog high pressure fogging humidification systems align with the ASHRAE standard requirements so that our systems can safely be used in all hospitals and healthcare facilities and environments.
As air handlers typically have air velocities of less than 750 ft/min (usually around 500 ft/min), the most common position for fog nozzle manifolds is inside the AHU itself. Occasionally, however, alternatives to a standard AHU installation must be resorted to. The simplest of these variations concerns not having enough space between the heating and cooling coil. However, nozzles can still be installed in tight spaces of less than three feet, sometimes requiring extra layers of mist elimination media at the droplet filter. Although this arrangement does increase water consumption, it provides a cost-efficient alternative to other, more energy-intensive forms of humidification.
In one Nova Scotia office building, for example, the existing electric steam industrial humidifier lacked the power to humidify the three-story building. Unfortunately, retrofitting the air handler with fog humidification also proved problematic as space was severely limited. Even with the air filters moved back 9 inches to provide the maximum available space within the air handler, the nozzles were still too close to the air filters. In this case, extra nozzles are required as more water will be eliminated at the droplet filter. If space is seriously restricted and the air handler cannot be extended by adding an extra section, another option is to place the fog manifolds in the ducting. As air speeds within the ducts are normally between 1000 and 1500 ft/min, although, it is necessary to increase the cross-sectional area of the duct to reduce airspeeds to below 750 ft/min (air velocities in excess of 750 ft/min can strip water off the back of the fog droplet filter and propel it into the ducting).
This was the case at one New York newspaper where the existing AHU was too small for the addition of fog nozzle manifolds and not easily modified. The solution was to enlarge a section of ducting to create a 500 ft/min air velocity area in which to set up the humidification hardware.
Buyers Guide to Industrial Humidifiers
Fog systems are more efficient than a steam industrial humidifier in part because they use excess heat in the return air to provide the energy needed to vaporize the water. A steam industrial humidifier has to supply all the energy required to vaporize the water. Another reason that fog systems are also more efficient is that they bring in less outside air when it is dry outside, so they save the water and energy required to humidify and heat the excess air.
Halifax Developments Ltd., for instance, owns a 1.3 million square foot commercial and retail facility in Halifax, Nova Scotia, where winter temperatures range from 10 to 30 degrees C. Due to increasing numbers of tenant complaints, the company decided to add a modern humidification system. Energy costs for an electric canister steam system were calculated at $48,000 per year, compared to $700 per year for fog. According to the company’s Chief Engineer, “Each of our seven fog units has paid for itself in eight to twenty-four months through reduced energy costs.”
Fog systems also provide evaporative free cooling, so less chilling is required as compared to steam commercial humidifiers. This is particularly true in areas with hot, dry climates. Fog humidification is not a complex technology when it involves an experienced fogging vendor. First-time users may require a factory start-up, where the fogging vendor comes in to ensure the installation is correctly performed, checks all the components, and conducts any final adjustments.