11 Ways to Improve Gas Turbine Fog System Performance
BlogIf you have one of the thousands of gas turbine inlet air fogging systems installed over the last 25 years then there is a good chance that you may need to upgrade your system to get it to run at peak performance and reduce maintenance costs.
Before upgrade After upgrade
Maintenance is key to produce efficient and effective fogging. Older parts need to be replaced or repaired and obsolete technology needs to be upgraded. Demand for renewable energy production caused increased demand for peaking power. This means power plants need state-of-the-art fogging systems more than ever. Here are 11 crucial improvements to make to boost your gas turbine fog system performance:
Modern high-pressure pumps require much less maintenance than older pumps
1. Seal-flushed pumps
Demineralized water causes rapid pump seal wear, resulting in frequent maintenance requirements. Upgrading to seal-flushed pumps can extend the seal life to 6,000 hours or more by circulating re-mineralized water through the cavity between the high and low pressure seals.
2. Water lubricated pumps
Upgrading to water lubricated pumps offers many advantages. They can run up to 8,000 hours between rebuilds and eliminate the need to change pump crankcase oil every few thousand hours.
The addition of high pressure filters and automatic drain valves can reduce nozzle plugging
3. High pressure filters
Pump seal wear introduces small particles into high pressure pipes, which can result in frequent fog nozzle plugging. High pressure filters, installed downstream of the pumps, capture these particles and can greatly reduce fog nozzle maintenance.
4. Duct drainage systems
Duct drainage systems should be capable of removing any flowing or pooling water from the duct so un-atomized water is not suctioned into the compressor. Some early installations did not include properly designed drainage systems. Viewing windows, to allow visual inspection of fog nozzle manifolds or the conditions at the compressor inlet can also be installed.
Some early systems have nozzle manifolds that don’t cover the full cross section of the inlet duct
5. Fog nozzle reconditioning
Nozzles should be visually checked annually to ensure proper operation. Mee Industries offers a nozzle reconditioning service to keep nozzles in top shape. Nozzles that cannot be reconditioned are replaced with new nozzles. Some operators keep a spare set of nozzles. This way nozzles in need of service can be quickly replaced, even during a short outage, and returned for reconditioning.
6. Correctly designed fog nozzle lines
It is important that nozzle lines distribute the fog nozzles across the entire airflow. If nozzles are not properly distributed some areas in the airflow can have more fog than can evaporate and other areas can have no fog. This can result in poor cooling performance, excess water accumulation on duct surfaces and temperature differences across the compressor inlet.
Upgrading old parts and technology means better performance and less regular maintenance
7. Stainless steel braided hoses
Replace old rubber hoses with high-quality stainless steel braided hoses and get maintenance-free operation for many years.
8. TIG welded nozzle adapters
In the early years of gas turbine fogging, fog nozzle adapters were often soldered or brazed onto the stainless steel fog lines. Over the years these joints have been known to fail. TIG welding creates a nozzle adapter joint that will last indefinitely.
Upgrading old parts and technology means better performance and less regular maintenance
9. Programmable logic controllers (PLCs)
Early fog systems often have PLCs that are no longer supported by the manufacturer, which makes reprogramming them impossible. MeeFog offers a PLC replacement that can be done in a few days in the field. Control software can then be upgraded.
10. Fogging at below base load
Early fog systems were designed to operate only when the gas turbine is above base load. If the gas turbine is often operated below base load this can be a problem. When the GT ramps up to base load, the fog starts and GT output spikes. To avoid this problem, the control software can be modified to allow for below base load operation of the fogging system.
Additional Wet Compression Power Boost
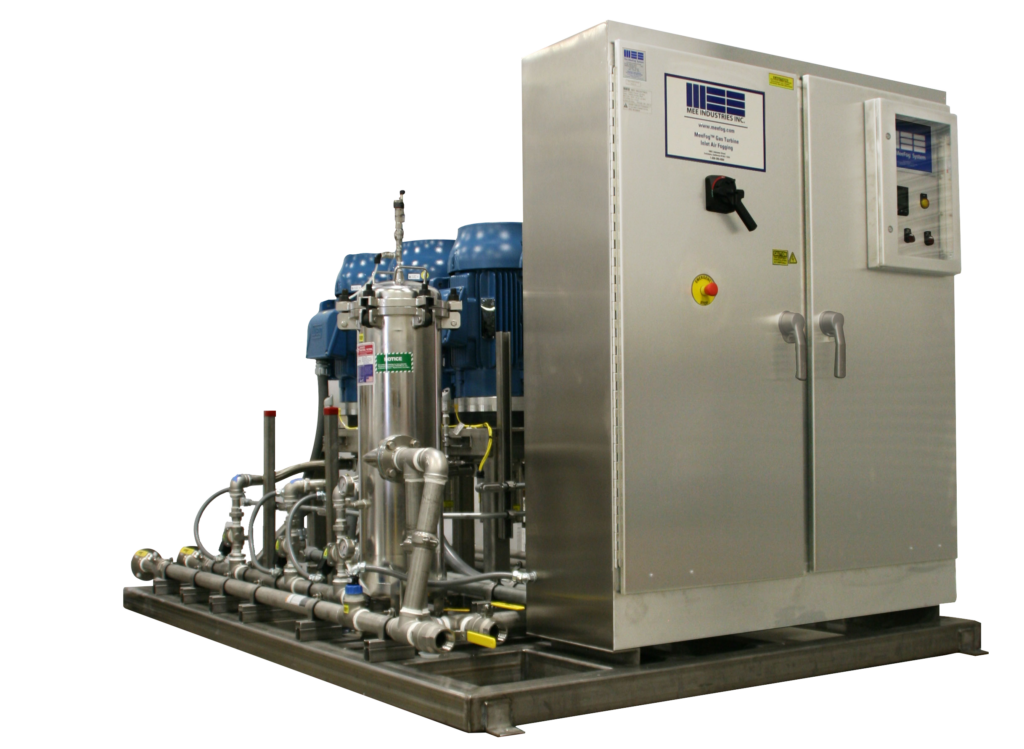
MeeFog wet compression skid
11. Wet compression for increased power boost
Wet compression consists of spraying more water into the inlet duct than can evaporate. The additional fog spray is carried by the airflow into the compressor where it evaporates and gives an intercooling effect. This reduces the work of compression so the turbine produces more power.
MeeFog has installed many wet compression systems on turbines ranging from aeroderivatives to modern F-Class turbines with fog flow rates of as much as 2.5% of the gas turbine air mass flow. Injecting 1% of the air mass flow as wet compression can produce a power boost of 5% or more, depending on the gas turbine.