Danfoss PAHT Pump Cuts Electrostatic Discharges and Energy Costs at Illinois Electronics Plant
Building Humidification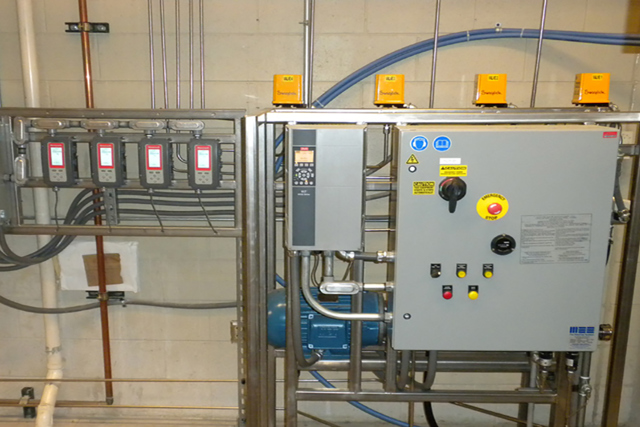
In a place where Midwestern winters keep average temperatures below freezing five months a year, controlling relative humidity to prevent electrostatic discharges (ESD) is a vital but costly part of producing advanced electronic circuitry. So Danfoss Power Electronics placed an intra-company call to Danfoss High Pressure Pumps to help them re-think their humidification technology and save big on energy.
Challenge:
Reduce the high energy costs of gas-fired humidification. Everyone who has walked across a carpet and touched a metal doorknob in a cold winter knows the problem: ESD is a shocking reminder of how low humidity affects our environments. As uncomfortable as ESD can be to our fingertips, its effects are even more devastating for sensitive electronic devices. ESD can cause serious damage to circuit boards when they are being assembled or handled.
That is why Danfoss Power Electronics installed six gas-fired humidifiers when it expanded its production facility in Loves Park, Illinois in 2009.
The wall-mounted system never worked as expected, however. Essentially a boiling pot of water and a fan to disperse steam, the gas-fired system could not provide a consistent humidity level around the plant. What is more, it accounted for an eye-popping 40% of the plant’s overall natural gas consumption.
Solution:
A centralized high-pressure fogging system that uses no gas and keeps humidity levels even throughout the factory. Andrew Keller of the maintenance department knew there had to be a better way, so he contacted Mee Industries to develop a fogging solution to replace the steam system.
Together, they configured a new system that suspended fogging nozzles from the ceiling throughout the plant. The nozzles are connected by pipe to a central high-pressure pump that maintains system pressure at 1000 psi during operation. Each nozzle creates a fine mist that evaporates within three feet, thus raising the air’s relative humidity reliably and consistently
everywhere in the plant.
The fogging system uses no gas whatsoever.
The Results:
Reliable, factory-wide humidification, lower energy costs and a $97k rebate. The new fogging system has proven its worth in more ways than one. For one thing, the new system is much better at distributing relative humidity evenly throughout the plant. Another benefit is reduced maintenance costs and increased reliability. Whereas the gas-fired system required frequent repairs with subsequent downtime, the centralized high-pressure system is relatively simple and easier to maintain. The biggest advantage of the new high-pressure system, however, is significantly reduced energy costs. The PAHT pump’s efficiency, further bolstered by Danfoss’ VLT®, has slashed energy costs by a stunning factor of ten. “Prior to our new fogger, humidification cost USD 8000 a year in gas and electricity. Now we pay just USD 750 in electrical costs for a better result,” says Keller.
“It’s not every day that you get a rebate of $97,236 from your utility company,” concludes Keller, “but it will be every year that we will be able to enjoy even, factory-wide humidity levels for a tenth of the cost.
Contact us to explore how we can help your facility save big on energy: