MeeFog Technology
Elegant Design with Unparalleled Efficiency and Reliable Performance
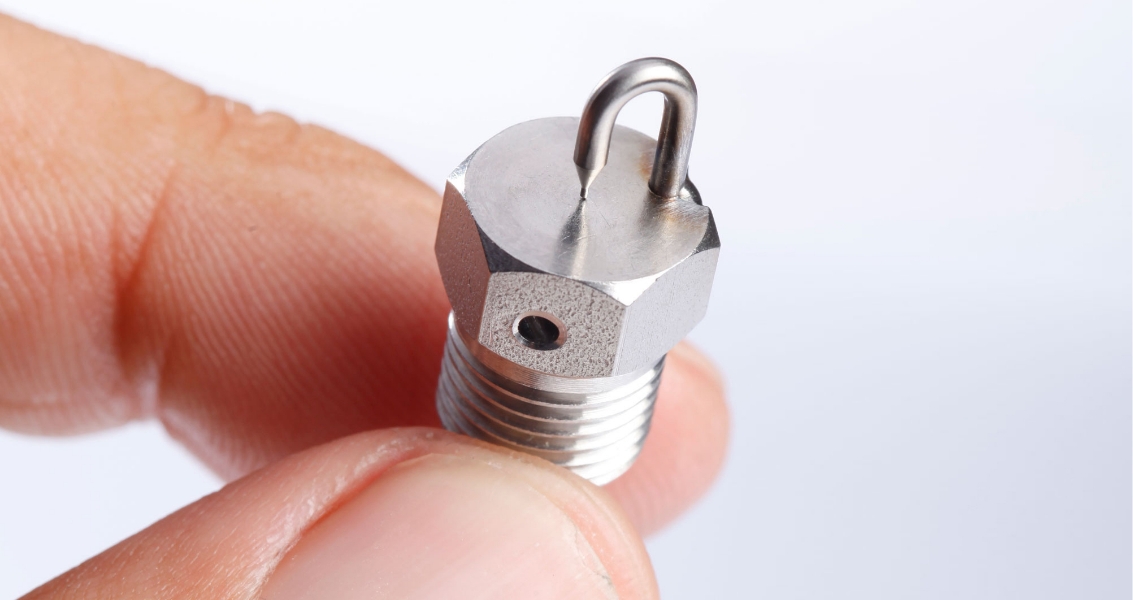
Each MeeFog system is designed using a series of high pressure pumps to pressurize demineralized water, which flows through a network of the highest quality stainless steel tubes. The water enters an array of proprietary Mee impaction-pin nozzles which feature a 150 micrometer diameter orifice to produce billions of ultra-fine droplets per second. At an operating pressure of 2000 psi, the average droplet size is far below 10 microns, or one tenth the diameter of a single strand of human hair. The resulting fog cools and evaporates more rapidly (as well as efficiently and economically) than any other fog method. Most importantly, a rapid return on investment for installing a MeeFog system can be realized.
Our Technology Per Industry
MeeFog Gas Turbine Inlet Air Fogging
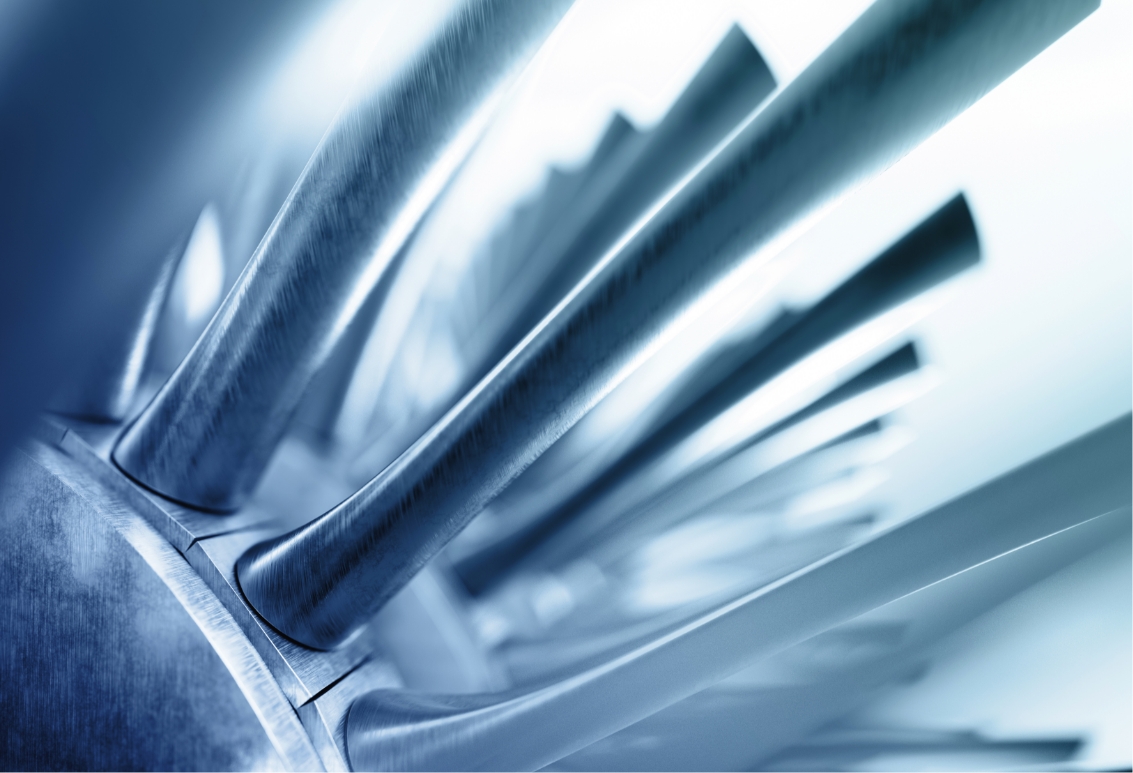
MeeFog systems have been installed on machines with 90,000 MW of gas turbine capacity. With over 1,000 systems installed, the total power boost from installed MeeFog inlet air fogging systems exceeds 9,000 MW. Fogging of a gas turbine engine is an art and a science, and there are several complexities that only our years of experience can address. Among our many repeat customers is a U.S. utility company that has installed MeeFog systems on over 60 of its heavy-duty gas turbines.
Mee Industries has worked closely with several utility companies worldwide to accommodate their special requests, accelerating delivery schedules to meet power crunches, and providing responsive after sales support. Our experience covers a wide range of heavy-duty and aeroderivative units ranging from 5 MW to 250 MW, and includes several projects with gas turbine OEMs.
Inlet Air Fogging Installation Diagram
Click the different areas of the diagram below to learn more information about our system.
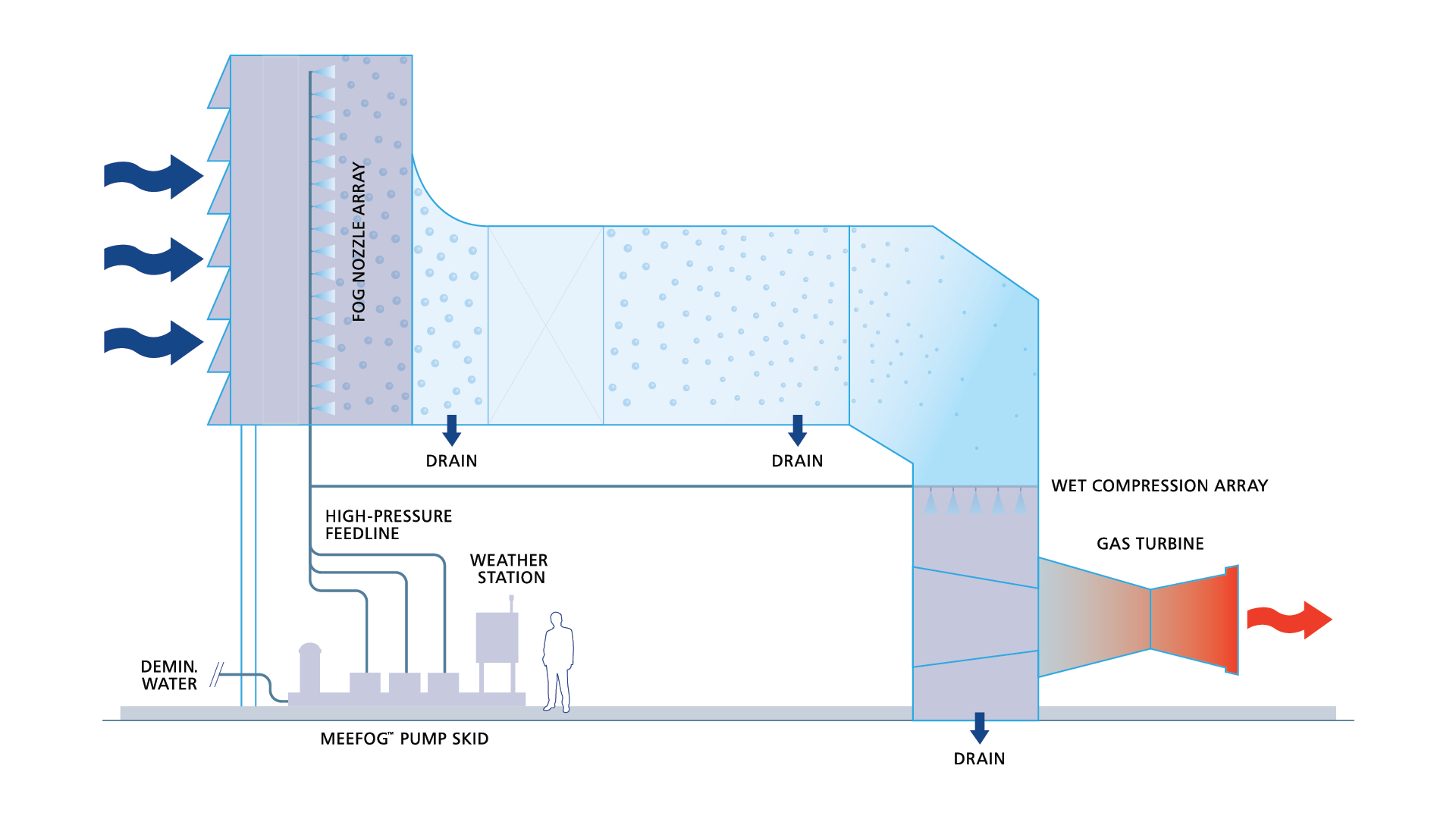
Pump Skid
Pump Skid
Stainless-steel welded frame with oversized inlet water filter. Water lubricated direct drive pumps means no oil or drive belts to change. Variable frequency drives are used to reduce flow for staging.
Evaporative Cooling Fog Nozzle Manifold
Evaporative Cooling Fog Nozzle Manifold
Cools to wet bulb temperature with droplets evaporating prior to entering compressor. Fog nozzles mounted on stainless steel tubing are wired for FOD avoidance. These precision nozzles are manufactured and tested in our own facility.
Wet Compression Nozzle Manifold
Wet Compression Nozzle Manifold
Fog droplets evaporate inside the compressor, giving an intercooling effect that reduces the work of compression. Water sprayed into the compressor will reduce NOx as well, but only about half as much as water sprayed into the combustors, because much of the air bypasses the combustion process.
MeeFog Commercial Humidification
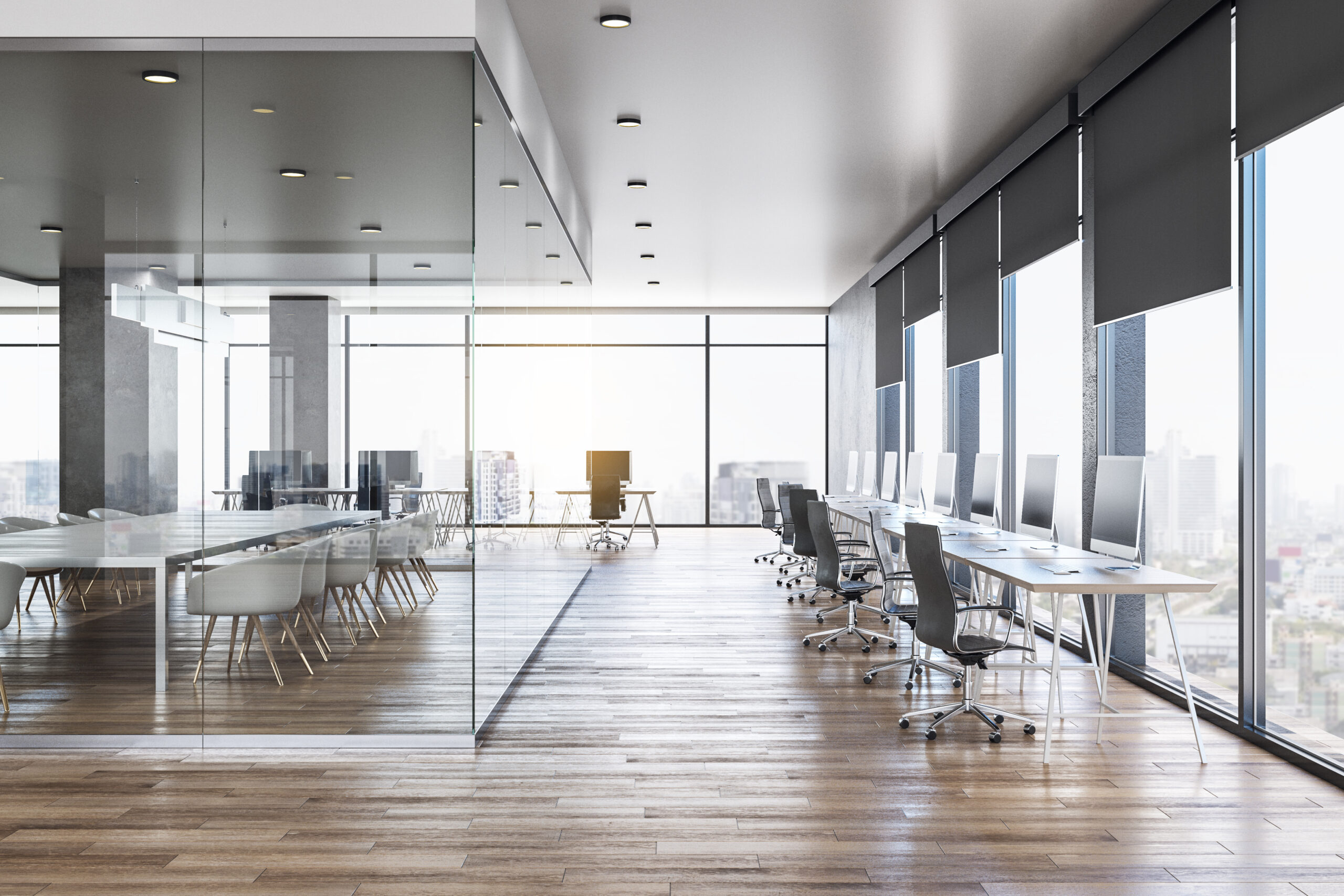
The MeeFog system uses high-pressure pumps to pressurize treated supply water to between 1000 and 2000 psi. The stainless steel MeeFog nozzles then atomize the water into billions of ultra-fine fog droplets.
MeeFog systems do not require compressed air or heat. Direct pressure means there are few moving parts (none in the air handlers or the humidified space). The energy consumed is a small fraction of that required by other technologies, such as compressed air, ultra- sonic, or canister steam systems.
HVAC Diagram
Click the different areas of the diagram below to learn more information about our system.
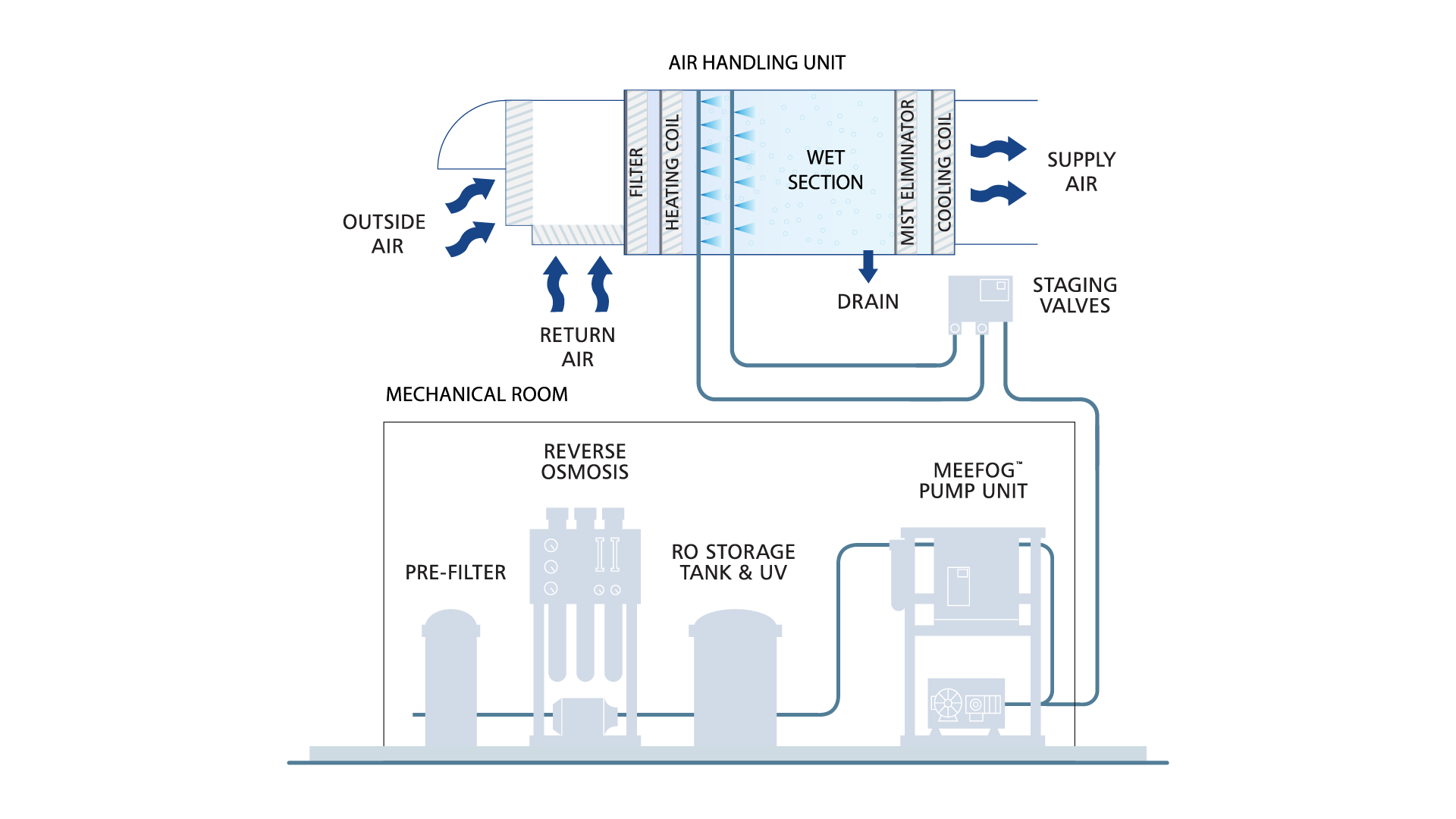
Reverse Osmosis Water Purification
Reverse Osmosis Water Purification
City water is treated using the Reverse Osmosis water treatment rack. This purifies the water, removing minerals, particulate, and microorganisms. Systems include automated membrane flushing, pre-treatment filtration, and UV Re-Circulation.
MeeFog Pump
MeeFog Pump
The high-pressure pump maintains 1000 psi water pressure in order to atomize the water into tiny droplets that can evaporate into the air stream. The pump rack has a VFD with panel-mounted controller that maintains pressure when staging valves open and close.
Staging Valves
Staging Valves
The valve panel allows precise control over how much humidification is injected into the air stream based on a signal from the BMS. It is possible to control the humidification level in the space to plus or minus 1% RH.
Nozzle Manifolds
Nozzle Manifolds
Fog nozzles are mounted on stainless steel tubing inside the air handler. These nozzles produce droplets in the 10-micron range. These precision nozzles are manufactured and tested in Mee Industries' own facility.
Mist Eliminator
Mist Eliminator
The mist eliminator removes water droplets larger than 5 microns. The filter pads can come off their stainless steel frames and can be washed or replaced easily.
MeeFog Humidification for Industry
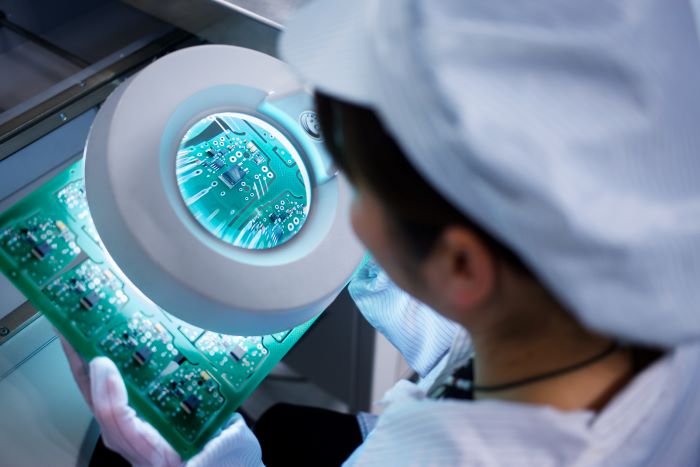
The MeeFog system is installed overhead in manufacturing areas. Industrial humidifiers are rapidly gaining importance in many industries. The requirements of modern industrial high-speed production techniques and increases in internal plant heat loads often result in the need for better control of humidity levels in the plant environment.
Other factors can affect humidity levels too. Upgrading manufacturing equipment can lower the humidity in a plant because modern machines often generate more heat. Many industries face stringent indoor air quality standards. Meeting these standards can often require bringing more outside air into the plant. If this outside air is dry or cold the result can be much lower indoor humidity levels. Existing plant humidification systems (humidifiers) are often incapable of meeting these increased demands, and adding more capacity to inherently inefficient humidification systems can be very costly.
The MeeFog system uses high-pressure pumps to pressurize demineralized water to between 1000 and 2000 psi. MeeFog nozzles atomize the water into billions of microfine fog droplets. The MeeFog industrial humidifier is an effective alternative to traditional more expensive methods of humidification. Most importantly, you’ll see a rapid return on investment for installing a MeeFog system.
In-Space Diagram
Click the different areas of the diagram below to learn more information about our system.
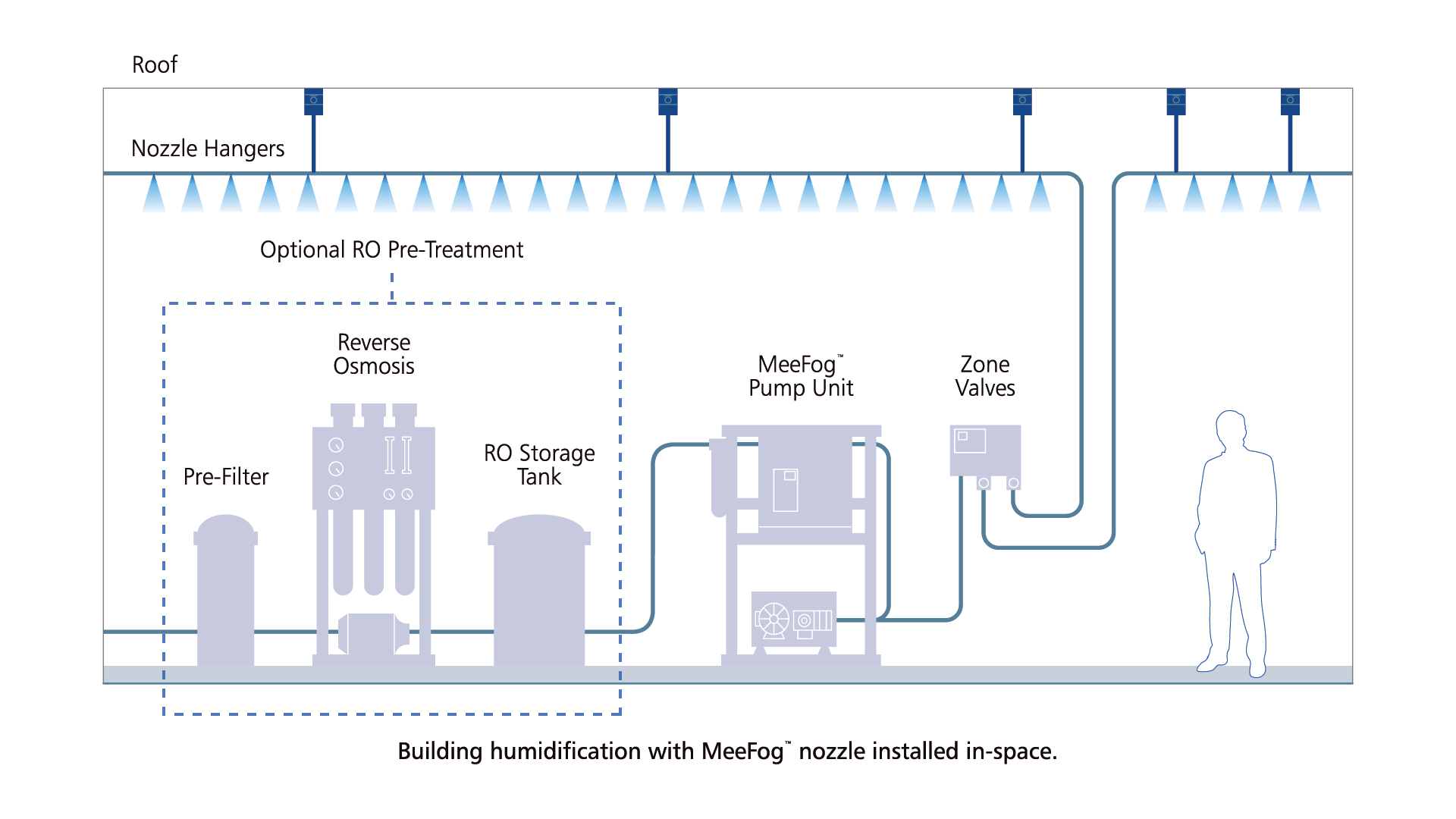
Water Pre-Treatment
Water Pre-Treatment
Basic water treatment, namely, a water softener is required for mineral removal. Based on dust-free requirements for the space additional components including reverse osmosis with automated membrane flushing and pre-treatment filtration can be added.
MeeFog Pump
MeeFog Pump
The high-pressure pump maintains 1000 psi water pressure in order to atomize the water into tiny droplets that can evaporate overhead. The pump rack has a VFD with panel-mounted controller that maintains pressure when zone valves open and close.
Zone Valve Panel
Zone Valve Panel
The MeeFog Zone Valve Panel provides control for up to five fogging zones. It can use an on-board humidity sensor or signal from other controllers to actuate ball valves that are slow acting to eliminate water hammer.
Swirl Jet Nozzles
Swirl Jet Nozzles
The MeeFog Swirl Jet nozzles are stainless steel with a .006” orifice and output 7 lbs. per hour of fog. Fog nozzles mounted on stainless steel tubing can be spaced one per 200 square feet or denser for areas with open bay doors or in need of higher humidity.
MeeFog Agriculture/Other
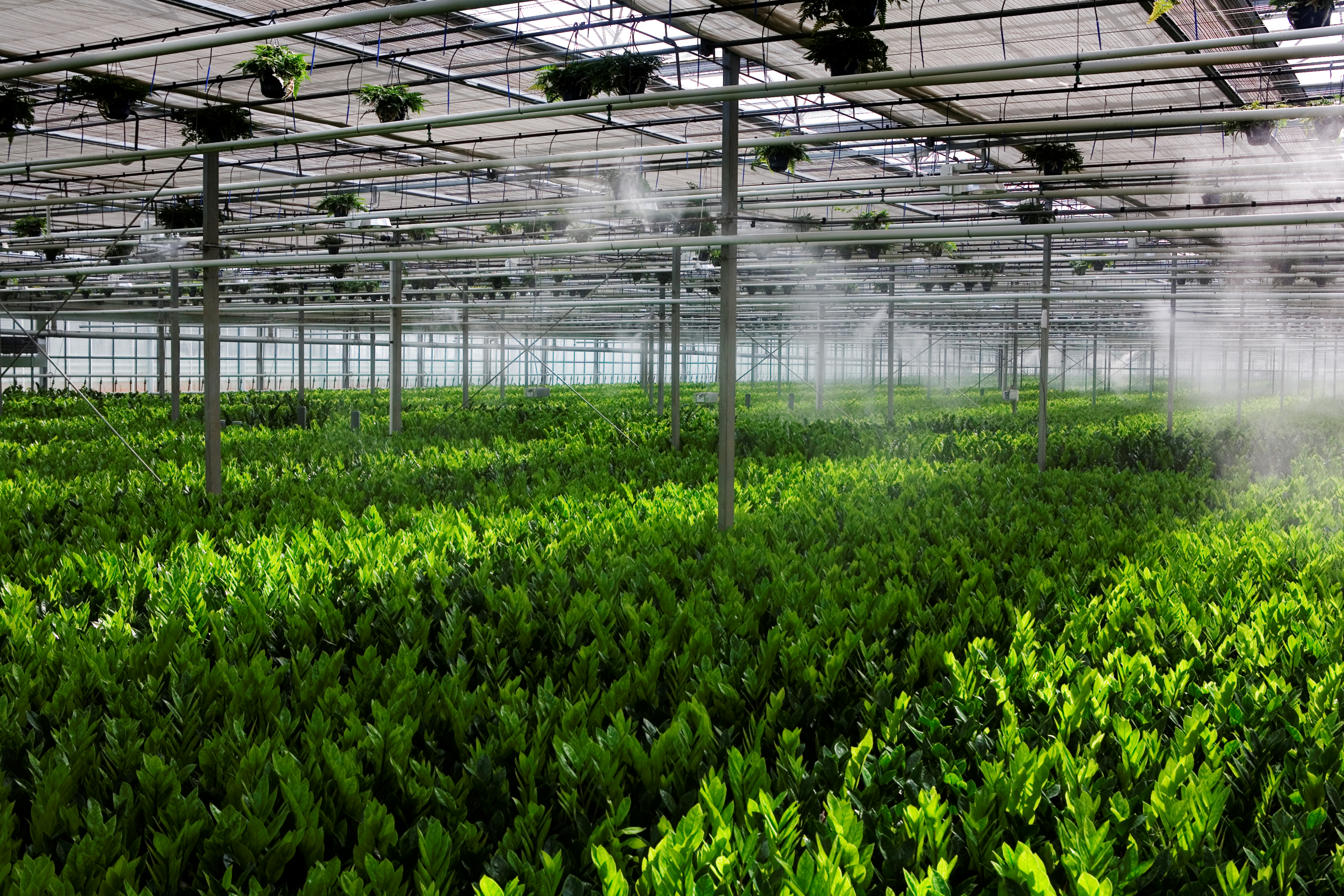
The MeeFog system generates high volumes of super small fog droplets. These droplets evaporate quickly and are ideal for agricultural applications that require evaporative cooling or humidification.
All MeeFog systems are custom engineered to fit the exact needs of each project. We analyze the supply water and design a water treatment system to ensure many years of low maintenance nozzle operation.
Imagine the nicest, most ideal environment you can. Imagine the ability to enhance your current environment to achieve that dream… imagine MeeFog.
MeeFog Special Effects
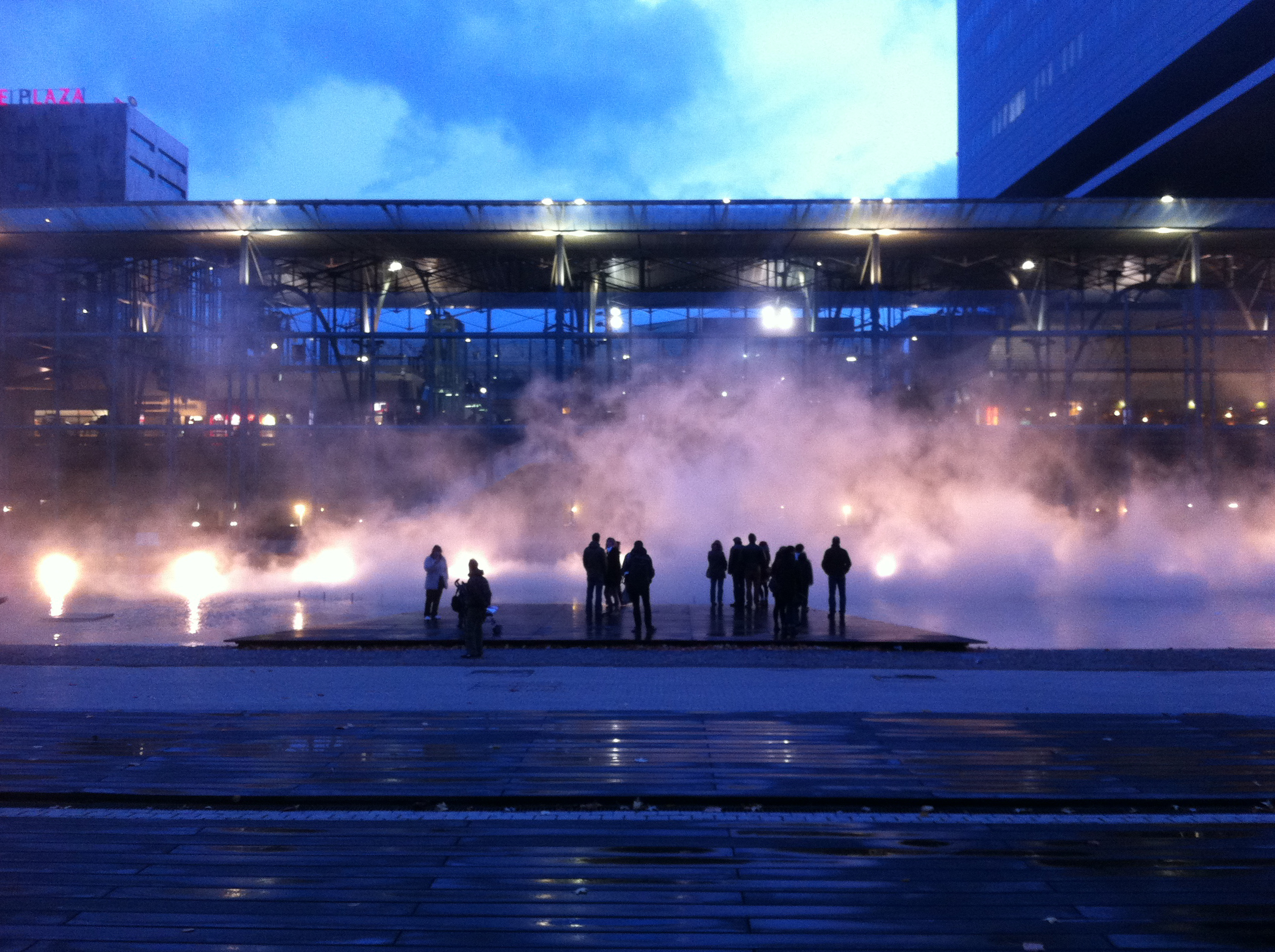
MeeFog Systems offer artists and designers innovative and robust aesthetic possibilities to create living and moving pure water fog effects with several methods for producing ultrafine fog droplets. Fog adds dimension and impact to a design, and it can be used to highlight and accentuate many design elements.
Mee Industries has a vision for the future that incorporates a firm commitment to quality research & development, product design, and continual excellence. No other company can compete with the depth of fog knowledge and approach to providing fog solutions that Mee Industries provides.